Analyzing unacceptable seal performance
Use this step-by-step process for seals
and other equipment
Patrick M. Flach, Mark J. Murphy, and William I. Anderson, John Crane
Sealol(R), Cranston, Rhode Island
Adhering to a disciplined approach to sealing system design and supporting
the selection with an ongoing action plan to improve the reliability of
sealed equipment dramatically improves mechanical seal performance. For
many years, acceptable seal performance was defined as minimal or no
visible leakage. During the last decade, these definitions changed
immensely while government and industry have worked to clean up the environment.
Conforming to new emission regulations is a reality that places greater
attention on seal performance and the seal selection process. An action
plan, when implemented in conjunction with the application of new standards
and guidelines, improves seal life while reducing emissions
Many users ask, "How do I determine if a mechanical seal is performing
acceptably, and what actions should I take if it is not living up to expectations?"
The answer involves a disciplined, problem-solving approach and, when necessary,
thoroughly reviewing the seal selection process. This action plan has eight
steps:
-
define acceptable seal performance,
-
troubleshoot the equipment in the field,
-
review the process and sealing system data,
-
select the sealing system,
-
investigate operational history,
-
perform seal analysis,
-
perform root cause analysis, and
-
implement solutions and
-
monitor results.
To improve sealed equipment reliability, look at the big picture in addition
to looking at each problem. Therefore, gather repair data for analysis
to yield useful information, such as determining the most common causes
of unacceptable performance and which equipment must be repaired most frequently.
In general, just follow the action plan below.
Define acceptable seal performance
Acceptable seal performance means conformance with published standards.
Federal, state, and local governments regulate maximum allowable emission
levels for a number of fluids. Users also create their own definition of
acceptable performance for fluids not covered by these regulations, or
when plant safety requires more stringent requirements.
Acceptability varies widely. Leakage from a clean water pump is usually
not considered unacceptable until it is visible and defined in terms of
measurable volume per unit of time. On the other hand, leakage of a volatile,
hazardous air pollutant from a piece of rotating equipment is probably
not visible and must be held to low levels.
The Society of Tribologists and Lubrication Engineers
was the first organization to address the selection process of mechanical
seals.
Leakage of volatile, hazardous air pollutants is measured by sampling the
environment adjacent to the equipment with a portable organic vapor analyzer
or sniffer. The allowable concentration is usually stated in parts
per million or even parts per billion.
Troubleshoot the equipment in the field
When a seal is not meeting expectations, troubleshooting the equipment
is the first step in improving the performance. It takes the straightforward,
common-sense approach. Focus on corrections that can be made on-site without
shutting down the equipment. Start with visual observations of the seal
and the seal support system. Determine the source of the leakage and, if
possible, correct it without removing the equipment from service. Typical
corrective actions include turning on a flush line, adjusting a quench,
tightening gland bolts, and checking pipe or tubing connections. Operational
corrections include opening a suction valve to stop cavitation or adjusting
a discharge valve to improve efficiency and reduce internal recirculation.
Review current process and sealing system data
If the performance cannot be corrected by actions in the field, then
take the equipment out of service. Before analyzing the equipment and sealing
system, however, review the current process and sealing system data as
well as the repair history for the equipment. Ideally, you have an extensive
database of information for each piece of equipment. The database should
provide information on the equipment, process fluid, operating conditions,
sealing system, and repair history. Entering the data into this database
establishes a baseline from which changes can be made and progress monitored.
The review may reveal that the conditions changed to the point that
the current sealing system cannot function reliably. In this case, select
a new sealing system.
Select the sealing system
If you determine that the sealing system needs to be changed--at this
stage or after finding the root cause of unacceptable performance-then
follow established guidelines in selecting the new system. Many users establish
seal selection standards based on plant experience. In addition, seal manufacturers
and users worked together to establish guidelines and standards that replace
or supplement a user's standards.
The Society of Tribologists and Lubrication Engineers was the first
organization to address the selection process of mechanical seals. They
published an "Application Guide to Control Emissions" in their Special
Publication SP-30 in 1990. Many users quickly adopted this guide for selecting
single, tandem, or double seals on the basis of specific gravity and permissible
emission levels. SP-30 was revised in April of 1994 based on the CMA/STLE
Mass Emission Study.
The revised document features an updated "Mechanical Seal Application
Guide" and gives insight into the use of contacting, non-contacting, and
dry-running seal technology. Since 1994, it has been adopted more widely
by the user community.
The American Petroleum Institute published the world's first mechanical
seal standard. Its intent is to identify the requirements of a sealing
system that will run at least three years and meets emission regulations.
It features a selection process for most refinery processes
and some chemical and general industry applications. As this standard
is revised, most likely it will address many more applications.
Investigate operational history
Modern control rooms gather a wealth of operational data. Find out
if deviations from normal operations could have played a part in causing
the failure. Items to check when investigating a failure include flows,
temperatures, tank levels, barrier pot pressures or levels, and motor current.Analyze
trends in these variables.
This data, however, does not replace the information gained by speaking
to the people responsible for operating the equipment. The operators will
not only be able to discuss any operational deviations, but they will also
know why the operation of the equipment deviated. For you to access this
valuable information, the operational personnel must want to help
solve the problem. Make them feel that they are a part of the solution
rather than a part of the problem. This is not always easy. You may need
to overcome years of finger-pointing among the operational, maintenance,
and engineering groups.
Perform seal analysis
Disassemble and carefully clean the mechanical seal for a piece-by-piece
inspection. Categorize each observation as being chemical, mechanical,
or thermal in nature.
Chemical damage is usually in the form of general corrosion, pitting,
corrosion-erosion (including fretting), or crevice corrosion under dynamic
O-rings. Also included is chemical attack of O-rings and the leaching of
the binder or secondary phase from the seal faces.
Mechanical problems develop from excessive hydraulic pressure which
cause face deflection, secondary seal extrusion, or erosion. Other mechanical
problems come from improper installation, uneven torque on gland bolts,
or misalignment.
Thermal damage to seal faces manifests itself as heat checking, carbon
blistering, pullout, setup deposits, polymerization between the faces,
or phonographing, the latter of shows up itself as a series of concentric
grooves. Coking, O-ring failures, and loss of spring load for bellows or
springs are also considered as thermal failures.
Grouping observations in this manner permits making a simple statistical
analysis that identifies the primary types of problems seen in your plant.
Record all observations each time a seal is evaluated if you want the database
to work effectively
Perform root cause analysis
Root cause analysis assigns the ultimate responsibility for unacceptable
performance. In other words, deduce the original cause of failure on the
basis of experience, troubleshooting, data gathering, and failure analysis.
For statistical purposes, organize the findings into nine primary causes,
then by secondary and tertiary causes. As an example, the first classification
may be "process" with a secondary cause being "poor lubrication" and the
tertiary cause being "flush flow blocked or reduced." Post to the database
each of the primary causes along with their secondary and tertiary causes.
Analyzing these root causes and the success of corrective efforts allows
making recommendations with a high degree of probability that the problem
will be fully identified and corrected.
Start monitoring upon commissioning the equipment
and continue under watchful eyes for the first 24 hours--the infant mortality
period.
Breaking down the root cause into primary, secondary, and tertiary causes
permits data to be statistically analyzed for an operating unit or an entire
facility, or to be expanded across many facilities. This improves reliability
in two ways. First it focuses attention on a particular piece of equipment
or a certain type of service. Second, provides the data that allows one
to look for general trends in the root causes recorded in the database
and comes up with an action plan to improve overall equipment performance.
For example, it makes sense to train operators if the root cause of a large
percentage of seal failures is operational issues.
As with any statistical analysis, good data is the key to success. Good
data is not always easy to obtain since the original cause of poor performance
is sometimes contradictory to one's instincts. For instance, it is common
to blame any dry-running pump situation on operator error. While this may
sometimes be the case, dry-running can also come from poor system design,
inadequate net positive suction head during startup, or it might simply
be more cost-effective to allow a pump to cavitate periodically. In these
cases, improve the system design or change the sealing system to make it
more tolerant of actual conditions.
Implement solutions and monitor results
The first step to implementation is documentation. Federal, state,
or local government regulations may require documentation of equipment
design or process changes. Implementing a Management of Change process
normally satisfies these regulations. At a minimum, this process requires
stating the reason for a change along with necessary drawings, installation
and operational procedures, updated files, and training. Once the change
is approved, the person responsible for implementing it should monitor
each step to ensure the process runs smoothly.
Start monitoring upon commissioning the equipment and continue under
watchful eyes for the first 24 hours--the infant mortality period. Installation
or operational errors are frequently the cause of failures that occur during
the first 24 hours. After the infant mortality period, continue monitoring
the reliability to be to ensure the implemented change produced the desired
result.
Analysis of data in the database
Use the repair database to look at the repair history for a particular
piece of equipment, to develop a bad actor list, or to determine
the most common root causes of repair.
When you pull a piece of equipment, look at the records for past repairs.
Doing so brings the analyst up to speed on problems that have been seen
before on this piece of equipment, as well as on solutions that have been
implemented to improve reliability.
Formulate a bad actor list by analyzing the repair data. Generate a
rudimentary bad actor list by finding the pieces of equipment that have
been repaired the most frequently during the chosen time frame. Include
in this evaluation other variables, such as repair costs and the criticality
of the equipment. In any case, generate a list of equipment causing the
most problems so time and effort can be focused on them.
The repair data also determines the most common causes of repair. To
do this, break down the root causes of unacceptable performance into categories
for analysis. The results of such an analysis are shown below.
Analysis of root cause data
Root cause data from five chemical plants and three refineries was
analyzed to determine the most common causes of repair. For statistical
purposes, the findings were organized into nine primary causes, then further
defined by secondary and tertiary causes. The nine primary causes are as
follows:
-
process,
-
maintenance,
-
equipment or piping,
-
scheduled maintenance and the equipment did not fail,
-
seal design or selection,
-
seal quality,
-
acceptable life-normal wear,
-
other that does not fit any of the defined categories,
-
cannot be determined.
A total of 4,133 equipment repairs were analyzed. The cause of failure
could not be determined for 553 of these repairs, while 104 others were
pulled for scheduled maintenance. This left 3,476 repairs to analyze statistically.
As shown in Figure 1, "process" was the most common root cause accounting
for 38 percent of the repairs. "Seal design or selection" and "equipment
or piping" were also significant contributors with 24 percent and 20 percent,
respectively.
Modern control rooms gather a wealth of operational
data. Find out if deviations from normal operations could have played a
part in causing the failure.
The root cause data was segregated by industry to see if there were significant
differences between the root causes of repair for oil refineries (Figure
2) and chemical plants (Figure 3). While the three most common root causes
were the same, the breakdown within these three areas differed significantly.
Process issues were more prevalent in the chemical plants, while equipment
and
piping problems were more common in the refineries.
To break down the analysis further, the secondary causes shown below
were analyzed for the "process"
primary cause:
-
operational upset,
-
poor seal face lubrication,
-
product setup,
-
other.
Analysis of the data shows that 53 percent of the "process" repairs were
attributable to "poor seal face lubrication" (Figure 4). This is obviously
an area requiring additional attention, so the tertiary causes associated
with "poor seal face lubrication" were further investigated. These tertiary
causes are:
-
air entrained in product,
-
cooling water flow blocked or reduced,
-
flush flow blocked or reduced,
-
heat tracing not working,
-
shutdown or startup,
-
barrier fluid level or pressure,
-
low flow recirculation,
-
low suction pressure,
-
other,
-
quench blocked,
-
recirculation flow blocked or reduced, or
-
suction screen blocked.
There were a total of 678 repairs caused by poor seal face lubrication.
Of these, 185 fell into the "other" category. This is obviously a large
percentage that needs to be reduced by revising the tertiary causes in
this section or by further training the analysts in choosing proper tertiary
causes. This analysis ignored the repairs that fell into the "other" category,
which left 493 repairs to analyze.
For statistical purposes, organize the findings
into nine primary causes, then by secondary and tertiary causes.
In order to narrow down these repairs into a more manageable number of
categories, the categories were grouped as follows:
Any cause for which a valve was closed or partially closed was put into
a category called "valve closed or reduced." This includes the causes "cooling
water flow blocked or reduced," "flush flow blocked or reduced," "quench
blocked," and "recirculation flow blocked or reduced." The cause "heat
tracing not working," which only accounted for three repairs, was also
included in this group.
The tertiary causes "low suction pressure," "air entrained in product,"
and "suction screen blocked," were put in a category called "NPSH available."
"low suction pressure" accounted for 122 of the 147 repairs in this category.
The results of the analysis are shown in Figure 5. The "valve closed
or reduced" and "barrier fluid pressure or level" tertiary categories can
generally be eliminated by a trained, diligent operator. The "shutdown
or startup," "NPSH available," and "running back on curve" categories,
on the other hand, can sometimes be more difficult to prevent.
Each of the other primary and secondary causes can be broken down similarly.
Analyzing the causes of repair leads to an action plan that can be formulated
to improve reliability on a plant-wide basis. A plant with a significant
number of repairs attributed to "seal design or selection" should consider
a seal standardization program to upgrade designs using the latest technology.
A plant with a high percentage of process related repairs, on the other
hand, should look into operator training programs as well as a plan to
encourage operators to "take ownership" of the equipment.
Improvements achieved
To quantify the rewards achieved when following this action plan, typical
improvements for a chemical plant and an oil refinery are shown in Figures
6 and 7. These improvements are shown as the percent increase in reliability
to remove any controversy regarding how
mean time between repair should be calculated.
This study used mean-time-between- seal-usage as the reliability measuring
stick. Every case in which a seal was used on a repair after the equipment
was installed in the field and turned over to operations was counted as
a repair or a seal usage. For example, if the equipment was taken out of
service for poor performance or high vibration, this was counted as a usage
even in cases where the seal never leaked. It would also be counted if
the same seal was reinstalled during the repair. On the other hand, a coupling
needing realignment was not counted.
Conclusion
A focused, disciplined approach is the key to improving equipment reliability.
Following this eight-step plan lets you implement a strategy to improve
seal performance. As shown in Figures 6 and 7, considerable improvements
are possible. In fact, the plants in this study experienced a steady overall
increase in reliability. In time, ongoing data collection can be used in
other studies. For instance, one can analyze the reliability improvements
achieved by converting from a component seal to a cartridge seal. This
could also be done for any other possible solutions. For example, this
data could be used in the future to answer the
long-standing question of whether a single seal is more reliable than
a dual
sealing system.
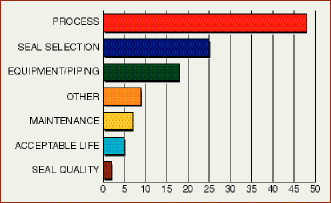
Figure 1: Breakdown of root causes for all plants
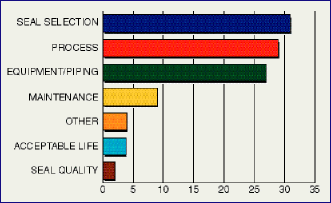
Figure 2: Breakdown of root causes for oil refineries
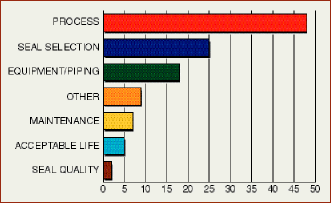
Figure 3: Breakdown of root causes for chemical plants
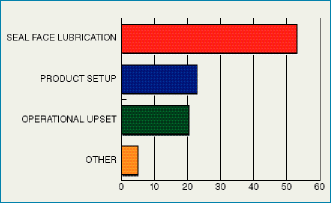
Figure 4: Breakdown of process root causes for all plants
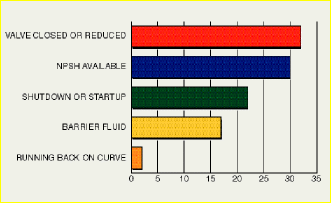
Figure 5: oor seal face lubrication breakdown for all plants
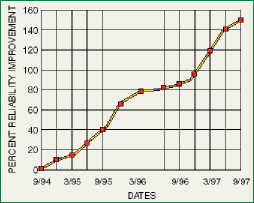
Figure 6: Reliability improvements at a U.S. chemical plant
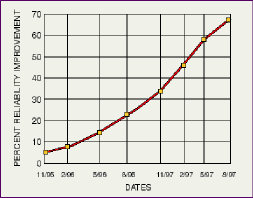
Figure 7: Reliability improvements at a U.S. oil refinery
This article, coutesy of the Turbomachinery
Laboratory Texas A&M University, College Station, Texas, was origianlly
published in the Proceedings of the Fithteenth International Pump Users
Symposium. You may contact the Turbomachinery Laboratory at http://turbolab.tamu.edu.
Copyright Turbomachinery Laboratory, Texas A&M University, College Station, Texas
|